Introduced for the first time at IMTS 2022, the Figur G15 is the first commercial platform of its kind to shape sheet metal on demand directly from a digital file. A software-driven ceramic tool on an XY gantry forms the sheet with up to 2,000 lbs of force in a highly engineered and proprietary build zone.
Figur’s patent-pending Digital Sheet Forming (DSF) technology eliminates the need for a traditional stamping press or custom tools, molds, and dies – delivering sheet metal forming that is accessible, flexible, and cost-effective, even at low volumes.
Preliminary Specs
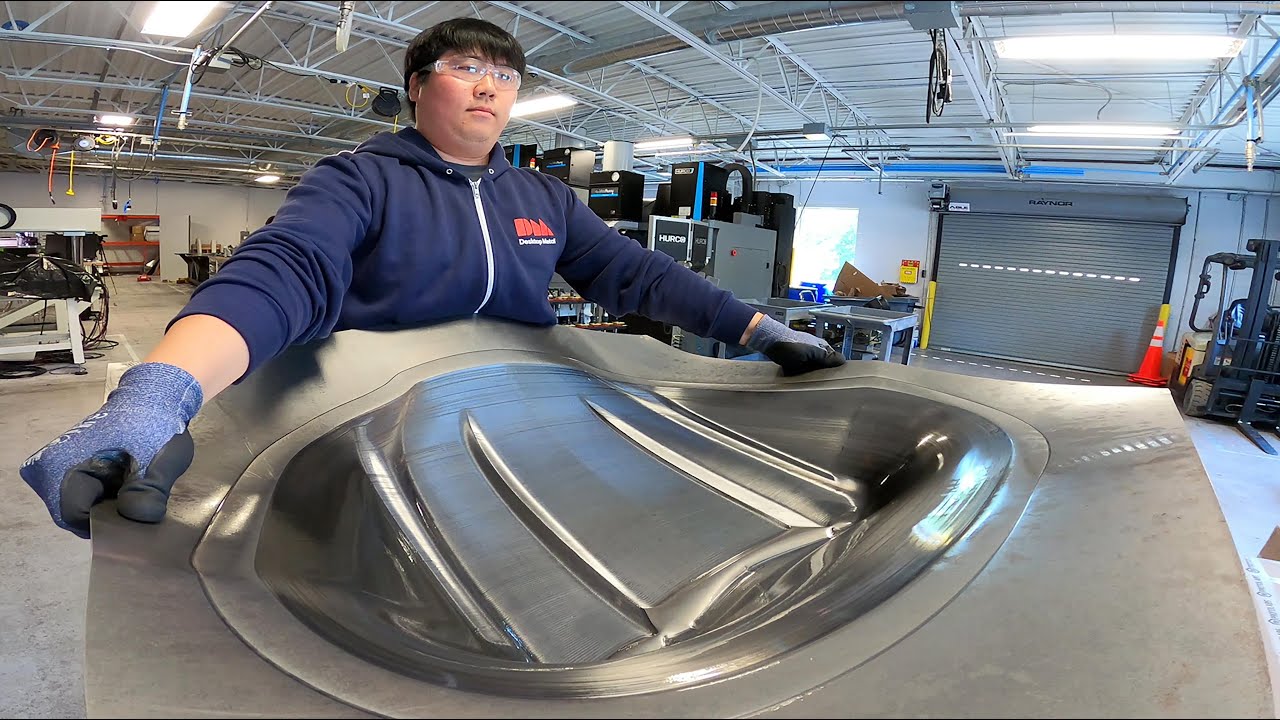
Digital Sheet Forming (DSF) Technology
The Figur G15 has an XY forming area of 1450 x 1000 mm and can process forms up to 400mm in the Z direction. A wide variety of metals and sheet thicknesses can also be processed – including steel up to 2.0 mm thick and aluminum up to 2.5 mm.
Competing processes are so expensive from a capital investment and time perspective that the payback for the G15 is fast for both manufacturers and suppliers seeking lower volume production or prototyping solutions. With the Figur G15, manufacturers can supply their customers with unique metal products quickly without high startup costs and long wait times.
For example, producing a common automotive exhaust muffler would typically require the purchase of a $150,000 die with a three month lead time. At a quantity of 1,000 parts, the cost per part for a runoff would still be about $160 per part including materials.
On the Figur G15, however, the same quantity of parts could be produced in weeks with an all-in part cost of approximately $10 primarily materials and labor. That’s less than 10% of the cost of traditional stamping with no lead time required.
Revolutionizing Sheet Metal Fabrication
Traditional sheet metal forming is a capital- and time-intensive process that requires an expensive stamping press, which often costs about $1 million, as well as tools and dies that take months to produce.
While similar processes such as hydroforming, fluid cell presses, and zinc low-cost die tooling aim to reduce the time of forming sheet metal, their benefits are relatively incremental and still out of reach for many companies.
Efforts to simplify sheet metal forming with digital approaches have focused on using robots deploying a tool to form sheets or using many tooling points that are digitally controlled.
However, a major challenge with these efforts has been controlling forming forces that radiate across the sheet metal as the force is applied at the tooling point, causing deformation of the sheet that is difficult to predict and impedes accuracy.
While digital sheet metal cutting is widely used today, and has delivered many benefits to the sheet metal forming and fabricating industry, no digital sheet forming solutions have been widely commercialized.
Figur’s breakthrough and patent-pending DSF technology is ready to unlock the benefits of digitization for sheet metal manufacturers, making them more agile and making sheet metal forms more accessible to new markets.
Industries
Automotive
Aerospace
Architecture and Construction
Consumer Products
Medical
Industrial
Contact Us
Interested in learning more about our products or services? Please reach out, we’d love to hear from you!